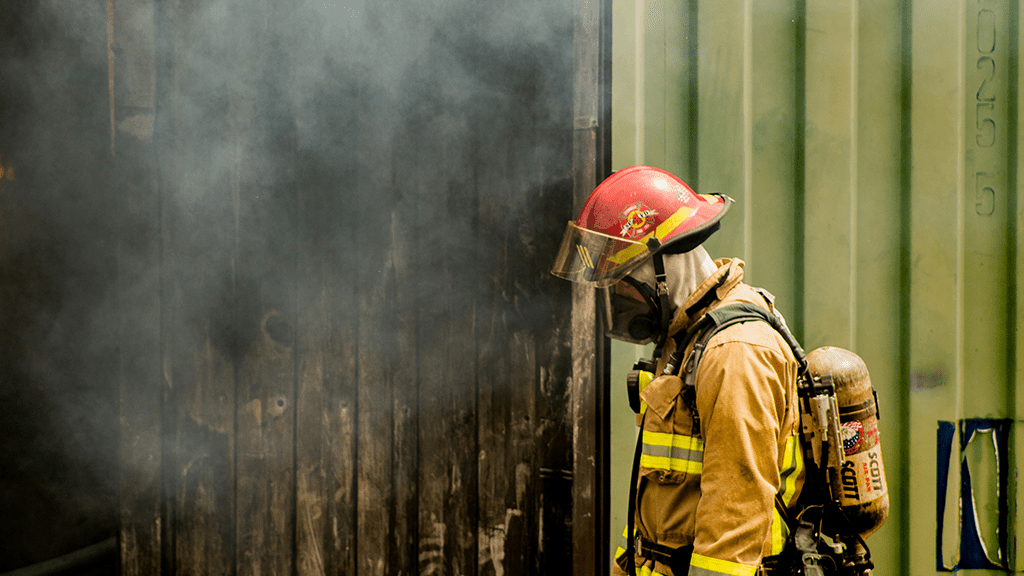
- August 31, 2025 3:17 am
- California
To satisfy application-specific requirements, design engineers in industries that manufacture sensitive components often require more agility than standard options for automating wet process cleaning equipment.
These specialized components can vary from chips, wafers, semiconductors, and electronic devices to the specialized optics for world-class lasers—the more intricate the equipment, the greater the necessity for more advanced adaptable cleaning alternatives.
Cleaning, an integral part of numerous manufacturing and maintenance processes, is often vital to the performance of a broad range of technologies and directs to the use of agents such as solvents, acids, or bases to terminate unwanted particulates and other contaminants. It also directs to the etching method utilized in semiconductor fabrication, where “cleaning” is the precision removal of thin layers of material.
Fortunately, a wide range of wet process equipment automation can more flexibly accommodate precise cleaning requirements. Modifying these automated cleaning tools to suit the application can cost-effectively improve process repeatability, throughput, and safety. In many circumstances, only minor editing to the standard equipment is essential.
Since its founding in 1982, JST’s mission has been to design and build efficient and cost-effective cleaning and processing products for cleanroom applications and support them with superior customer service. They strive to “be the best at what they do.” The company cares about their customers and products. It is a dedication to customer satisfaction with over thirty years of JST design and manufacturing expertise which is the foundation of their business. JST is a complete service design and manufacturing company. Capabilities include Process Development and Applications Testing, Engineering Design and Drafting, Manufacturing, and Final tests. Their product lines include Wet Processing Equipment, Precision Cleaning, and Cleanroom Accessories & Support Equipment.
JST’s manufacturing expertise includes plastics, metal fabrication, and mechanical and electrical assembly. They design modular systems that allow easy access to process and maintenance areas. Every product is thoroughly tested and packed in their certified Class 100 Cleanroom. JST’s state-of-the-art facility is headquartered in Boise and encompasses over 60,000 square feet. The latest technology is used to cut and form raw materials, whether plastic or metal. Certified welders fabricate the parts, which are leak-tested and cleaned before mechanical and electrical assembly.
Experienced technicians assemble the product, making sure to conform to the Semiconductor S2 Guidelines for high tech design Safety, National Electric and Fire Codes and any local codes that may apply. All JST equipment is built to withstand the rigors of an industrial environment, from industrial-grade PLCs and electronic components to the structural integrity of their welded fabrication. Each piece is quality built for endurance which has earned JST a reputation for consistently manufacturing equipment that exceeds industry standards for safety, reliability, and performance.
Automating cleaning processes allow customers to repeat a given result consistently. It increases throughput and product yields. Automation software allows for tracking many products through a production line and accurately collecting data throughout the process. It provides a repeatable quality result where defects or excursions can be quickly identified and remedied.
Concerning safety, JST’s equipment processes with a variety of hazardous chemicals. Removing the operator interface through automation of chemical management (delivery & waste) provides a much safer work environment. Most customers understand the value of automating chemical management.
JST’s most significant advantages to their customers is their ability to maintain a leading position in designing and manufacturing wet process and precision cleaning equipment. This offers customers the latest technology as well as:
Over the previous two decades, there has been a significant focus on outsourcing to minimize costs through just-in-time (JIT) inventory. With the supply chain overwhelmed with orders and not enough staff, the ability to vertically integrate has become a necessity to overcome material shortages to stay on schedule. “Lead-time is the most pressing concern from most customers and being able to quickly adapt and produce products is an advantage.” says Sam Bertagnolli, VP of Sales & Marketing of JST. “JST’s historical ability to customize products has created an environment where agility and flexibility are rewarded. The ability to do rapid prototyping helps maintain the agility and flexibility required in the current economic climate.”
Alongside the dedication of resources and planning to develop a state-of-the-art applications laboratory adds a feather to the very well-accomplished cap for JST. In addition to the dedication of resources, JST’s state of the art applications laboratory with complete metrology equipment allows us to analyze data in real time for faster results before or concurrent while working on design and preproduction processes.
JST takes an inside-out approach to all its designs. They begin with the physical parts, substrates, or wafers to be processed and then design the system around the desired throughput and physical property requirements. The company recently launched multiple mass wafers and single wafer transfer systems on the front end of its process equipment including vertical stocking of multiple lots. They have reduced the operator interface of handling these parts through a variety of automation platforms.
A prime example is customers who manufacture a wide range of microelectronic products for a variety of Industries: 5G, Cloud, Automobile, Energy, IoT (Internet of Things), Aerospace, Defense, and Microelectronics in General. Their production lines relied heavily on manual wafer processing of multiple substrate sizes and materials. JST’s ability to automate these processes to remove many manual operation functions has given this specific customer a real advantage in producing a quality product on time and with higher yields. Through automation of chemical management, they have reduced safety concerns and experienced significant cost savings through the management and tracking of chemical procurement and disposal.
JST has been growing by partnering with European Market Partner (EMP) in Europe, nFort Technology, Taiwan, and MYG-Tech, Israel. The partnership will combine JST’s diverse portfolio of innovative and customizable wet chemical processing and cleaning benches with EMP, MYG-Tech and nFort’s knowledgeable support for customers in Europe, Taiwan and Israel for the semiconductor, IoT, MEMS, and optoelectronics market. “We are excited about our partnership with EMP in Europe, nFort Technology, Taiwan and MYG-Tech, Israel,” states Ryan Zrno, CEO at JST Manufacturing, “to see what the future brings not only for the partnership, but, more importantly, our customers.” For the road ahead, JST wants to continue investing in Research & Development via their Clean Room Applications Laboratory, improve processes, throughput, and yield, meet customers’ demands and allow them to evaluate systems before purchasing.
" They strive to “be the best at what they do.” The company cares about their customers and products. "
Sam Bertagnolli
VP Sales & Marketing
JST Manufacturing