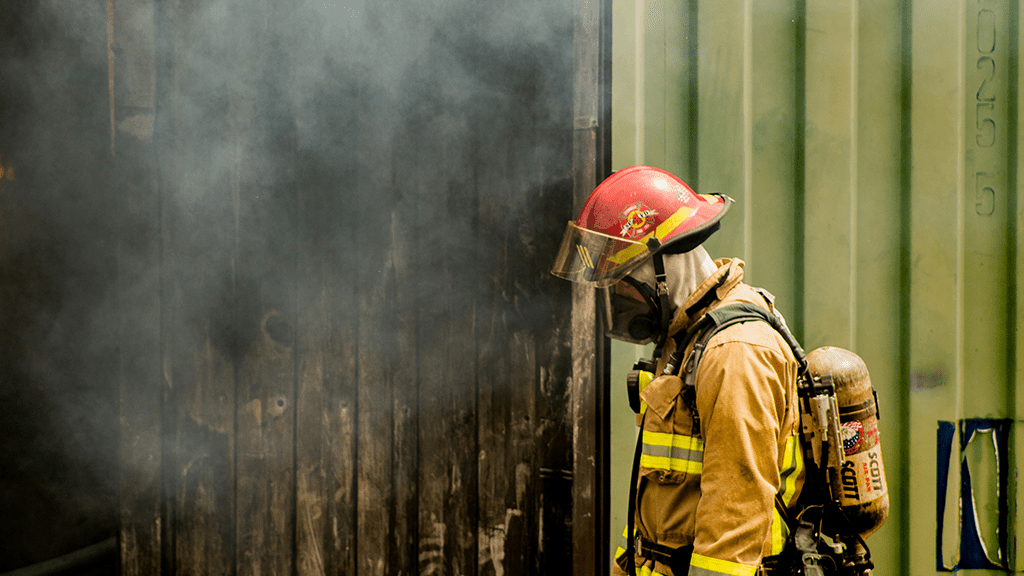
- July 2, 2025 10:21 pm
- California
Plex was born on the shop floor of a factory making axles, pinion gears and drive shafts. Our founders are the workers who kept the presses running and made sure parts matched customer specs. Frustrated with inaccuracy and breakdowns, they built Plex to make the plant run better. Plex rapidly expanded to support a wide range of discrete manufacturing operations from metal formers to food and beverage companies. The Plex Smart Manufacturing Platform now connects every manufacturing operation in the cloud for maximum efficiency, productivity and visibility, while supporting continuous innovation.
Plex was acquired by Rockwell Automation in September 2021. “We built Plex walking between the shop floor and the boardroom, figuring out what we needed to track, measure and automate, then updating the software and iterating again. This model of continuous innovation still serves as the foundation of Plex solutions today,” says Jerry Foster, Plex Co-founder and Chief Technology Officer.
The Plex Smart Manufacturing Platform was built to deliver the four key capabilities required of manufacturers and Industry 4.0—Connect, Automate, Track and Analyze. With these four capabilities, you realize greater control with high levels of enterprise visibility and quality guarantees.
The Plex Smart Manufacturing Platform works by tying all your people, technologies and machines together to create a complete, connected view of the entire business. In doing so, Plex becomes a digital system of record and engagement that radically improves your visibility into what’s happening, what’s about to happen and what just happened. Plex doesn’t just make manufacturing smart, it makes you smart about your manufacturing business. If producing high quality products is a high priority, Plex will help you make them more precisely and efficiently.
Plex will also improve the speed and accuracy of your operation while helping you reduce waste. We slash the time you’re forced to spend meeting industry requirements like audits—often from weeks to mere hours. That, in and of itself, gives you a degree of control and efficiency that was, until recently, unthinkable.
Customer Satisfaction
Since its first press started running in the 1960s, metalstamper E&E Manufacturing has prided itself on its ability to engineer and manufacture quality components efficiently and cost-effectively.
The auto supplier invested in its first ERP system, a QAD product, in 2005. Within a few years, the company realized that the on-premise software didn’t include the comprehensive functionality it would need to achieve its planned growth.
Like most ERP tools at the time, the QAD system was focused primarily on financials and didn’t include functions to support operations. For example, it wasn’t able to automate scheduling, track inventory accurately, or minimize the cost of quality. These constraints required E&E to develop and rely on additional homegrown databases, internal systems and manual spreadsheets to supplement its ERP.
Senior management began to explore options for upgrading or replacing QAD and its other disparate databases and systems, but those plans got put on hold as all manufacturers faced another more pressing challenge: the economic downturn.
E&E stopped upgrading to new releases of its existing QAD on-premise system during the downturn. It didn’t want to devote the expenses, time or human resources needed to manage the required customizations.
The metalstamper also put off server upgrades and purchases, despite the fact that the existing servers were near capacity and E&E’s database was continuing to grow rapidly.
After the company emerged from the downturn, the game was back on and senior managers focused once more on the “upgrade or replace” dilemma.
They looked first at what it would take to catch up to the latest QAD software version and server capacity requirements. What they learned was disturbing: before they could even begin the costly customizations needed for the new QAD versions, they would have to purchase “customization codes” from QAD – another set of expenses. And the functionality would still not meet the company’s growth needs.
As the projected costs of maintaining its limited legacy system continued to climb with every new question management asked, E&E shifted its focus entirely on the search for a new solution.
After reviewing several cloud-delivered and on-premise ERP systems – including a cloud-delivered option from QAD – E&E Manufacturing chose to launch Plex, a cloud solution designed by and for manufacturers. The company implemented the solution at its two facilities in Plymouth, Michigan and Athens, Tennessee in under a year.
“We knew we needed a more comprehensive robust solution, but we didn’t intentionally set out to find one that is cloud-delivered,” said E&E Manufacturing CFO Brian Swanson.
“QAD also offered us a cloud-delivered system,” Swanson noted. “It appeared to be almost identical to its on-premise solution except we’d be renting the servers from QAD. Plex is totally different. It’s clear from how it operates that Plex is a true cloud model and was developed to optimize the benefits of cloud delivery.”
Plex’s upfront cost for implementation was lower than what E&E would have paid for QAD or any of the other solutions it considered. Also, while QAD’s cloud solution would have required additional annual fees in addition to monthly subscription costs, Plex doesn’t require an annual fee.
“In total, we are saving $50,000 a year in systems costs with Plex.”
“That savings includes not just the flat cost of Plex over our previous ERP solution but also its replacement of the six or seven systems and databases we’d been using for functions ranging from HR to Engineering to preventive maintenance,” said Swanson.
With Plex, E&E’s scheduling is more accurate and timely. Improved scheduling, in turn, drives better communication between the plant floor, billing and maintenance.
Plex’s traceability functions have also enabled the company to tighten up inventory management.
“We can track every packaged container in each lot, and that’s greatly improved the accuracy of our inventory tracking,” explained Swanson. “Before Plex, we usually needed to adjust our annual inventory by about $70,000. Now our adjustments are negligible – around $15,000 or less.
Today on the E&E plant floor, Plex-generated quality checksheets must be completed before any job is run. The system randomizes the details on the checksheets, ensuring they are carefully reviewed for each job.
For each operation, if the associated checksheet isn’t completed, the machine stops production. The checksheets require supervisor sign-offs. If something is out of spec, the supervisor won’t sign off on the part, and this prevents any quality issues or production delays.
Before, with manual operator checksheets and a manual process, it was hard to catch quality issues until the problems had grown.
Plex’s checksheets and other controls on the plant floor have enabled E&E to reduce its scrap, rework, delays and other factors that contribute to the cost of quality. The measurable results are impressive.
Within just the first year of launching Plex, the company reduced its Cost of Quality (CoQ) by 42 percent.
The Future of Manufacturing
Jerry in an article in Forbes talks about why manufacturers were hesitant about technology investments but not any more! “Earlier this year, I attended a conference called Integr8, which showcased the impact of Industry 4.0 (I4.0) in manufacturing. There were countless booths with attendees talking about I4.0 initiatives and selling I4.0 solutions such as additive printing, artificial intelligence (AI) and robotics. It was exciting to see because the manufacturing industry and its leaders haven’t always been as fast to embrace new technologies as they are today. In fact, historically, manufacturers have been hesitant to adopt new technologies, skeptical of the return on investment (ROI) and the necessity of such projects. Today, that point of view is waning in manufacturing—whether out of necessity or greater access to proven technology—and the industry, now more forward-looking than ever before, is exploring endless possibilities provided by I4.0 technologies. In fact, 83% of manufacturers believe that smart manufacturing is key to future success.”
To understand why manufacturers are historically hesitant to adopt new technologies. In the ’90s, the manufacturing landscape was changing, and the outlook was bleak. Industry conditions at the time led manufacturers to be more reactive than proactive. At the same time, supply chains were becoming increasingly global. As a result, competition led to unparalleled cost cuts for suppliers. On top of all this, labor disputes were contentious, and manufacturers were facing massive layoffs.
Obviously, manufacturers were enduring turbulent times that would shape the industry for decades to come. As a result, manufacturers became very focused on bottom-line margins and maintaining revenue during times of fierce competition and price cuts. This made them skeptical of any new technologies or processes that didn’t have quantifiable and immediate ROI, and many feared technology trials were expensive science projects with no proven outcome.
While enterprise technology has advanced far beyond where it was in the 1990s, many of the same industry challenges continue to plague the manufacturing industry today: supply chain volatility, labor issues and shrinking profit margins.
This time, supply chain volatility is being caused by market closures and facility shutdowns as a result of Covid-19. Labor issues have arisen and their work remotely. Last but certainly not least, on the list of challenges, profit margins are decreasing once again, now as a result of consumers’ and businesses’ inability to purchase products due to shortages caused by facility/source shutdowns or consumers being unable to purchase products in stores.
This time when faced with these challenges, the manufacturing industry largely took a different approach. The manufacturers that thrived during the turbulent pandemic were those with strong leaders who realized the value of I4.0 technologies ahead of time.
Now, manufacturers recognize they can’t wait decades for new solutions and processes to become standard within the industry. As a result, we’re witnessing manufacturing transform from a reactive and conservative industry into one that’s proactive and aggressive in its exploration of new technologies.
Although the manufacturing world around us is weathering another storm, I4.0 technologies’ ability to weave digital threads through facilities like never before is driving manufacturers to transform their internal environments to meet the demands of a modern external marketplace. Technologies, such as process automation, advanced analytics and traceability for inventory and resource planning and remote-work-friendly technologies, including cloud and automated production management, enabled manufacturers to maintain business continuity during the pandemic. Now, manufacturers who have already embraced I4.0 are already exploring the next generation of manufacturing technology, like machine learning and artificial intelligence.
Manufacturers will gravitate to different I4.0 technologies depending on their specific environment, supply chain, products and customers. There are too many I4.0 technologies and capabilities to list in this article, but there are several exciting new technologies driven by augmented reality (AR) that can provide quick and measurable ROI to manufacturers.
Augmented, or extended, reality is a necessary technology for the future of smart manufacturing. One of the most immediate and easily achievable ROIs involves the use of AR-based, rather than paper-based, work instructions. Digital instructions can be superimposed on worksites through AR technology or spoken to workers through headphones—eliminating the need to move back and forth between paper instructions and the job at hand. Digital instructions can effectively reduce the number of errors made by workers, although the proportion of error reduction will depend on the manufacturer’s industry and environment.
More innovative and industry-transforming technologies will arrive sooner than you think. Non-manufacturing companies already recognize this. One of the most-visited vendors at the Integr8 conference this year was a gaming company that is advocating using its metaverse engine to develop compelling manufacturing solutions.
Manufacturing leaders that have not yet embraced I4.0 would be wise to follow their innovative counterparts’ lead, or they might be left behind—only to be seen in the rearview mirror of modern, smarter manufacturing. If you don’t already have a strategy in place for IT transformation at your facilities, consider connecting with an expert to identify your business needs and develop a strategy to successfully leverage I4.0.
" Our purpose is to forever change how the manufacturing world leverages technology to drive business results. "
Jerry Foster
CTO
Plex Systems